We’re experimenting with turning on comments on our Substack. Please leave your thoughts below! We’re also hosting a Stripe Press pop-up coffee shop and bookstore on Saturday, June 28, in Washington, DC. RSVP here if you can make it.
At the bottom of the periodic table, you’ll find the ‘heavy’ atoms. Their tiny nuclei are crammed with over a hundred protons and neutrons. Heavy atoms, like uranium-235 are naturally unstable. The electrical repulsion inside them is so great that they are perpetually on the edge of fragmenting – a single, slow-moving neutron is enough to make a nuclear rupture.
When the break comes, the ‘heavy atom’ will split into two mid-sized atoms, commonly pairs such as krypton and barium or strontium and xenon, along with a few neutrons. Each split also releases about 200 million electron-volts of energy; a gram of U-235 yields roughly the heat of a few tonnes of coal.
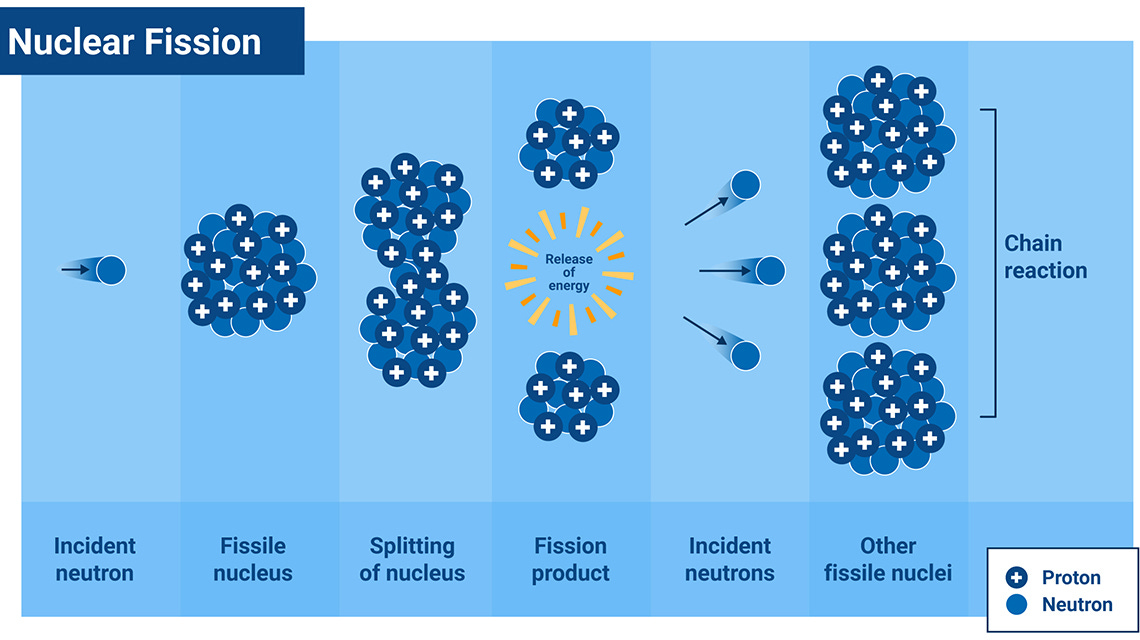
Meanwhile, the neutrons generated by each split can strike other heavy nuclei, triggering a carefully managed chain reaction. The steady torrent of heat this process generates is used to boil water, produce the steam that spins turbines, and generate electricity.
If you are interested in nuclear energy, you will hear throwaway references to different reactor types. To an outsider, it may not be obvious how the many types of water or gas reactor projects differ from each other or which experimental designs are likely to be close to fruition. This post outlines the main categories of reactors, their advantages, drawbacks, and the prospects for different concepts.
The different reactor types have some features in common. They need nuclear fuel containing fissile material, usually uranium that has been enriched to contain a higher proportion of fissile isotope uranium-235. Most reactors also have a moderator that slows the flying neutrons so they linger near the uranium nucleus longer, allowing it to absorb them more easily and keep the chain reaction going. Cooling systems then transfer heat from the reactor core to turn a turbine and generate electricity while preventing overheating (which would cause a meltdown of the core).
They key differences across reactors tend to concern:
Moderator: Different moderators slow neutrons with varying efficiency. All moderators absorb a proportion of the neutrons, but every absorbed neutron is a neutron that cannot fission a nucleus, making it harder to keep a chain reaction going. Moderators with lower absorption rates can use less enriched or entirely natural uranium.
Coolant: The coolant establishes the maximum operating temperatures and pressures. When the steam is at a higher temperature, a higher proportion of its energy is converted into mechanical work turning turbine blades, meaning it has a higher thermal efficiency. Some coolants have more failsafes, preventing meltdowns, or minimising their impact if they do happen.
Fuel composition: The form and enrichment level of fuel determines energy density, frequency of refueling, and the amount and type of waste that’s produced.
I’ve not focused on size in this piece, as many of the reactor types in this piece could theoretically be built either as large reactors or adapted to smaller and modular designs, often known as SMRs. Currently, the most common basis for SMRs is the pressurized water reactor, although essentially every experimental design is currently being approached in a small format for economic reasons.
Operating reactors
Pressurized water reactor
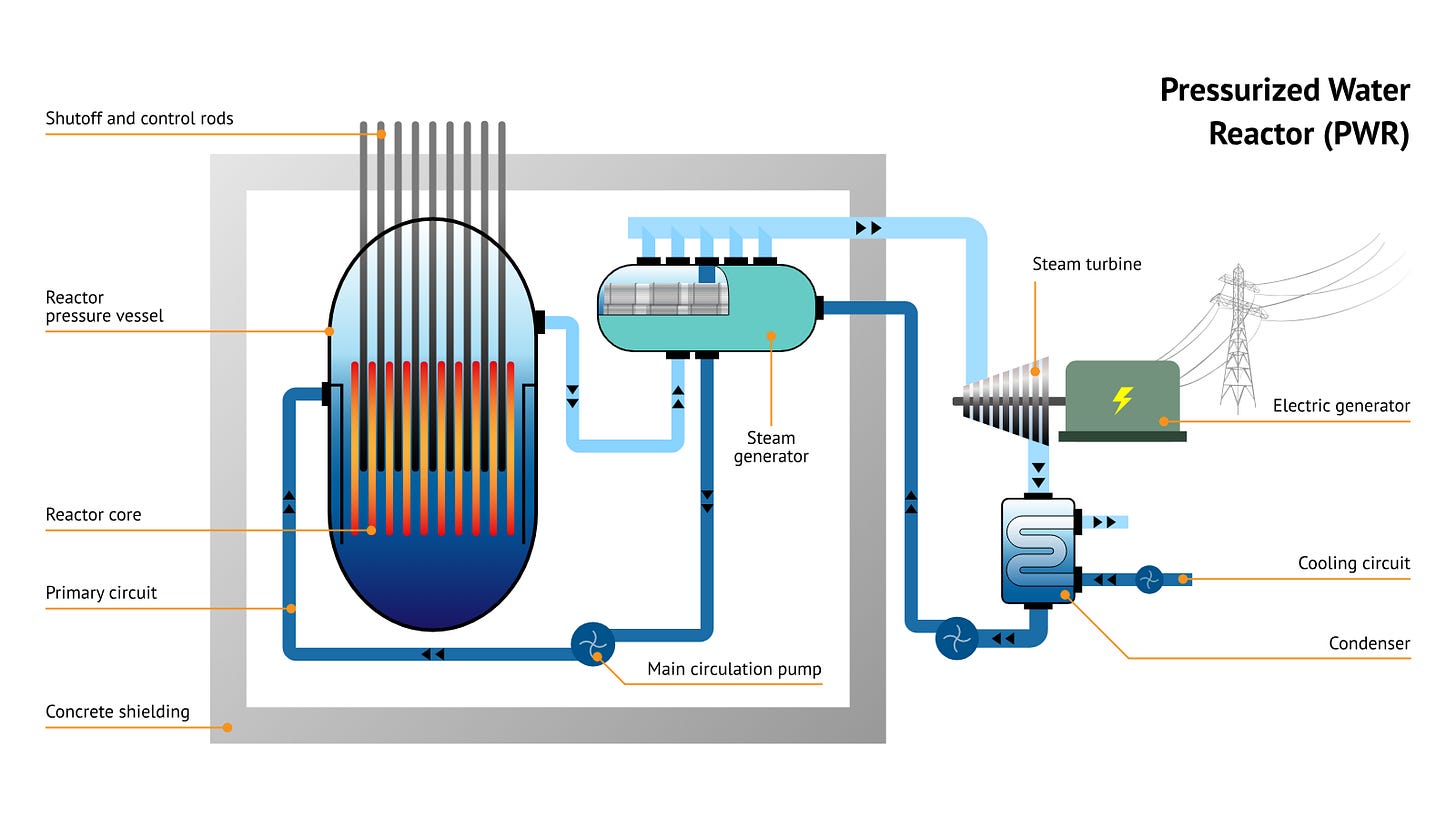
Moderator: water
Coolant: water
Operating temperature: 290-330 celsius
Thermal efficiency: 33 percent
Enrichment: 3-5 percent
The Pressurized Water Reactor (PWR) is the most widely used nuclear reactor design in the world. Roughly 70 percent of operational civilian nuclear reactors are PWRs. The vast majority of reactors in France, South Korea and China are PWRs, along with two thirds of the US fleet.
In a PWR, nuclear fission heats water in a primary coolant loop kept under high pressure to prevent boiling. This pressurized water transfers heat through steam generators to a separate secondary loop where water is allowed to boil and produce steam, which then drives turbines to generate electricity.
First developed in the US to power submarines, they were adapted and scaled up for civilian use as part of the 1950s Atoms for Peace program, with the first commercial PWR beginning operation at Shippingport, Pennsylvania in 1957.
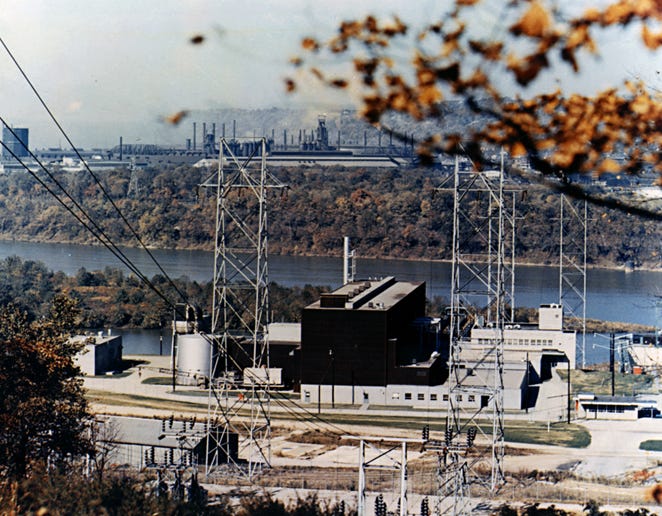
The PWR’s dominance was driven by two main factors.
First, its military origins ensured that there was a readymade industrial base for civilian deployment. Companies like Westinghouse that designed and built reactor components for military purposes already had equipment, supply chains, and in-house expertise.
Secondly, the use of water came with inherent advantages. As the reactor gets hotter or if any coolant is lost, the nuclear reaction slows, acting as a passive safety measure. This is because water becomes less dense as it heats up, making it less effective at slowing down neutrons to the optimal speed needed for uranium fission. This is known as a negative temperature coefficient and is an example of ‘passive safety’, when natural physical processes build in a degree of safety without the need for human intervention.
The two-loop design also creates a barrier between the radioactive primary coolant and the turbine system, making maintenance easier and reducing the number of components that need radiation shielding.
Despite their dominance, PWRs do have notable disadvantages, which have inspired much of the subsequent innovation in reactor design. The pressure level of 150-160 bar (one bar is roughly equal to atmospheric pressure; 150 is roughly the crushing pressure that would be experienced under the weight of a 1,500 metre column of water) requires highly robust pressure vessels and piping, along with a rigorous inspection regime. The two-loop design also builds in a degree of complexity.
Water also has its drawbacks, most notably its lower steam temperature. This means that PWRs typically achieve lower thermal efficiency than most of the competition, with only about a third of the heat generated being converted into electricity. (This is less of a problem if there is some other use for the spare heat, for example a district heat network as at Beznau in Switzerland.)
Boiling water reactors
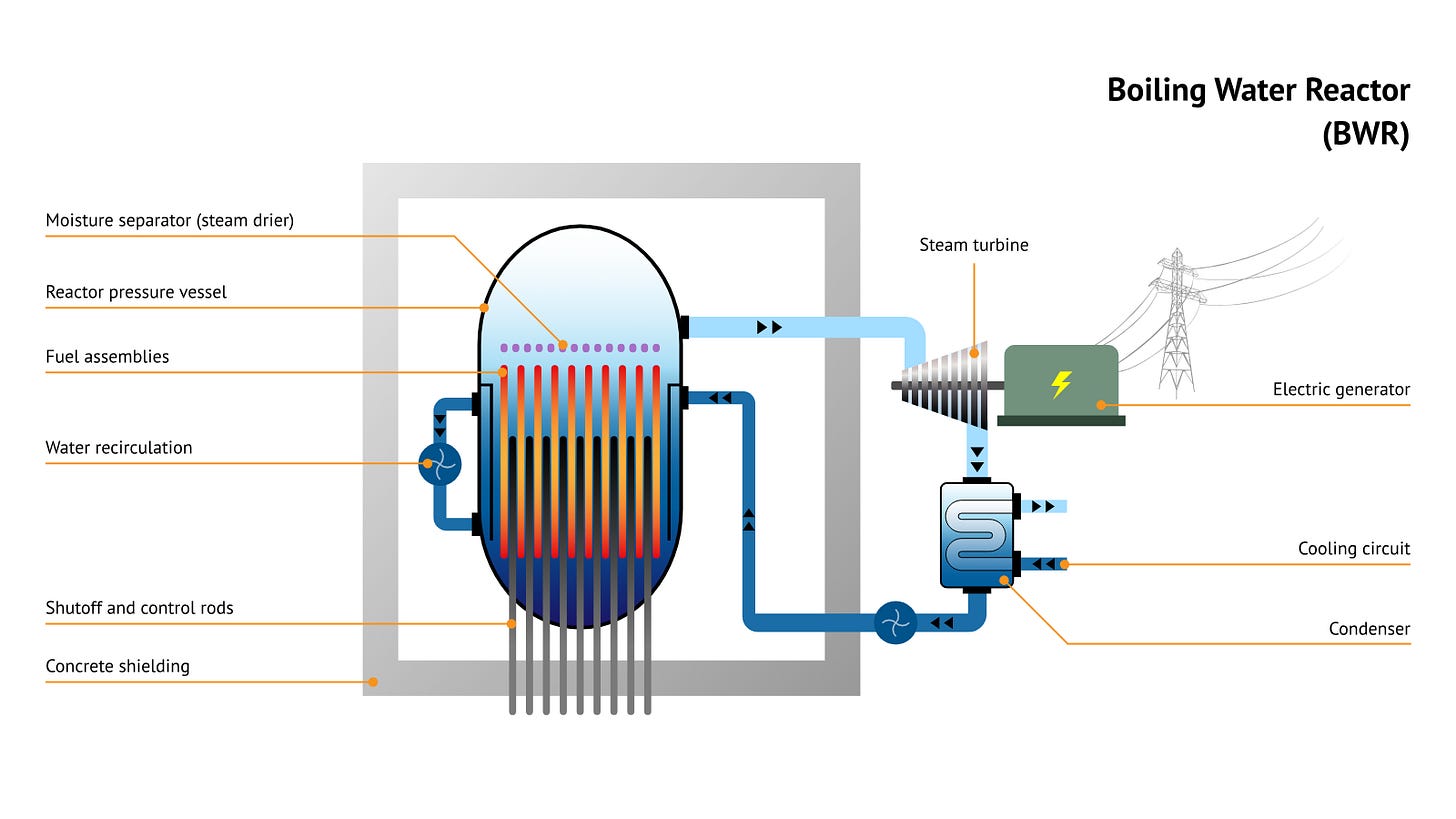
Moderator: water
Coolant: water
Operating temperature: 288 celsius
Thermal efficiency: 35 percent
Enrichment: 3-5 percent
The Boiling Water Reactor (BWR) is the second most common nuclear reactor worldwide, accounting for roughly a fifth of nuclear power generation. In a BWR, water circulates through the reactor core where it is heated directly by nuclear fission until it boils, creating steam that drives turbines to generate electricity. Unlike PWRs, BWRs employ a single-loop design where the same water serves as both coolant, moderator, and then boils directly inside the reactor core to generate steam.
Developed in the 1950s by General Electric, BWRs emerged as an alternative to PWRs with the first commercial unit entering operation at Dresden, Illinois in 1960. Their development was driven by the pursuit of simplified systems and lower construction costs. Alongside the US, major BWR adopters include Japan, Sweden, and Germany.
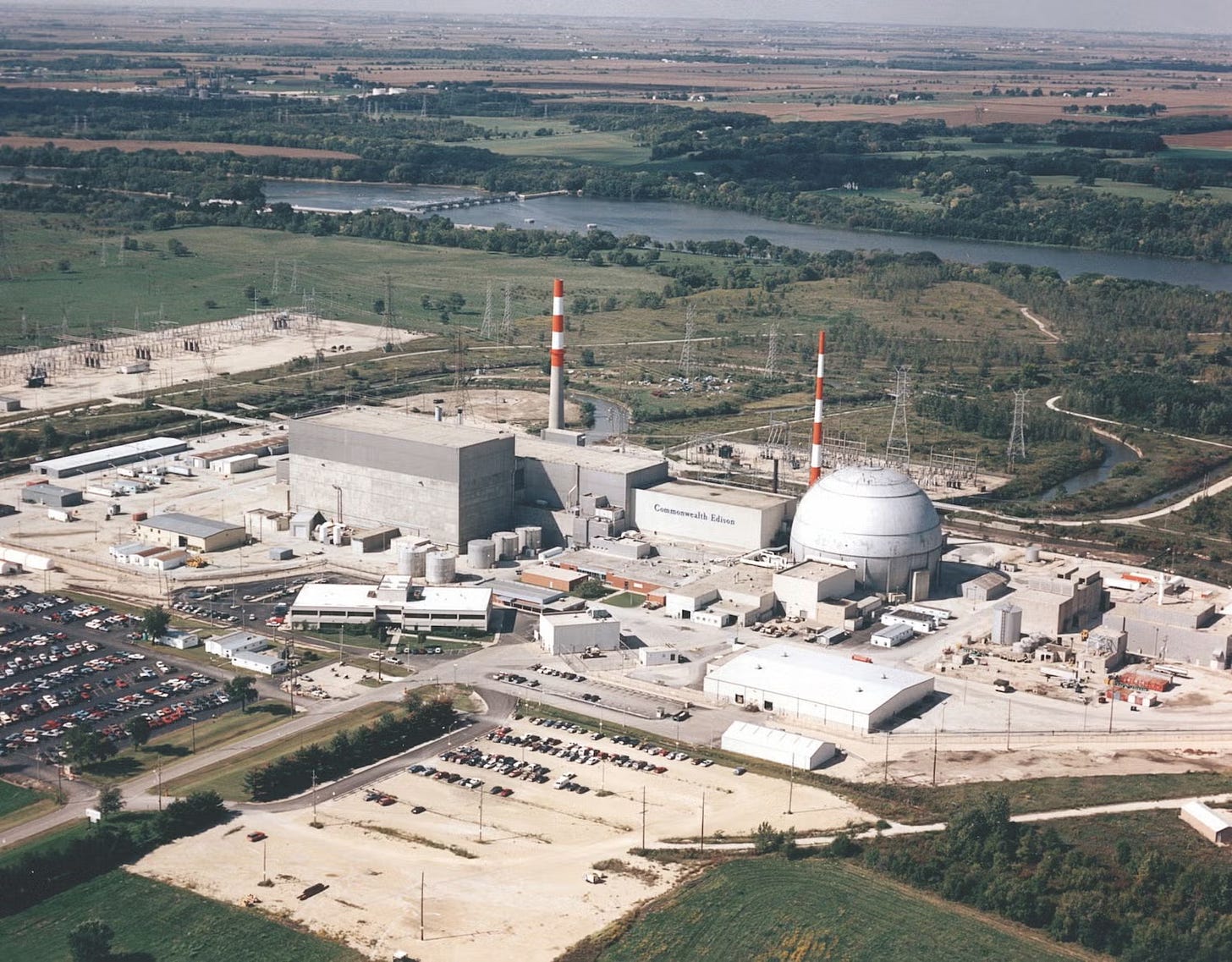
BWRs offer several advantages compared to other reactor designs. By employing half the operating pressure of a PWR, the BWR does not need such thick pressure vessels and demands fewer pressure-resistant components. The single-loop design strips out some complexity, while retaining some of the passive safety benefits of water. The steam in a BWR is generated directly by boiling conditions in the reactor core, which removes some of the temperature and efficiency loss. This means that despite operating at a lower temperature than PWRs, thermal efficiency is marginally higher thanks to higher steam quality.
Despite these benefits, BWRs face certain disadvantages. The single-loop design means radioactive water comes into contact directly with the turbine system. This means that all the components require radiation shielding and makes maintenance more complicated. BWRs also need complicated control systems, because steam bubbles can displace the liquid water moderator, potentially causing the reactor’s power to oscillate and interfering with cooling. Additionally, when steam forms in the upper part of the core, it creates uneven heating patterns that operators must carefully manage to prevent any areas from becoming too hot and maintain stable operation.
Pressurized Heavy Water Reactor
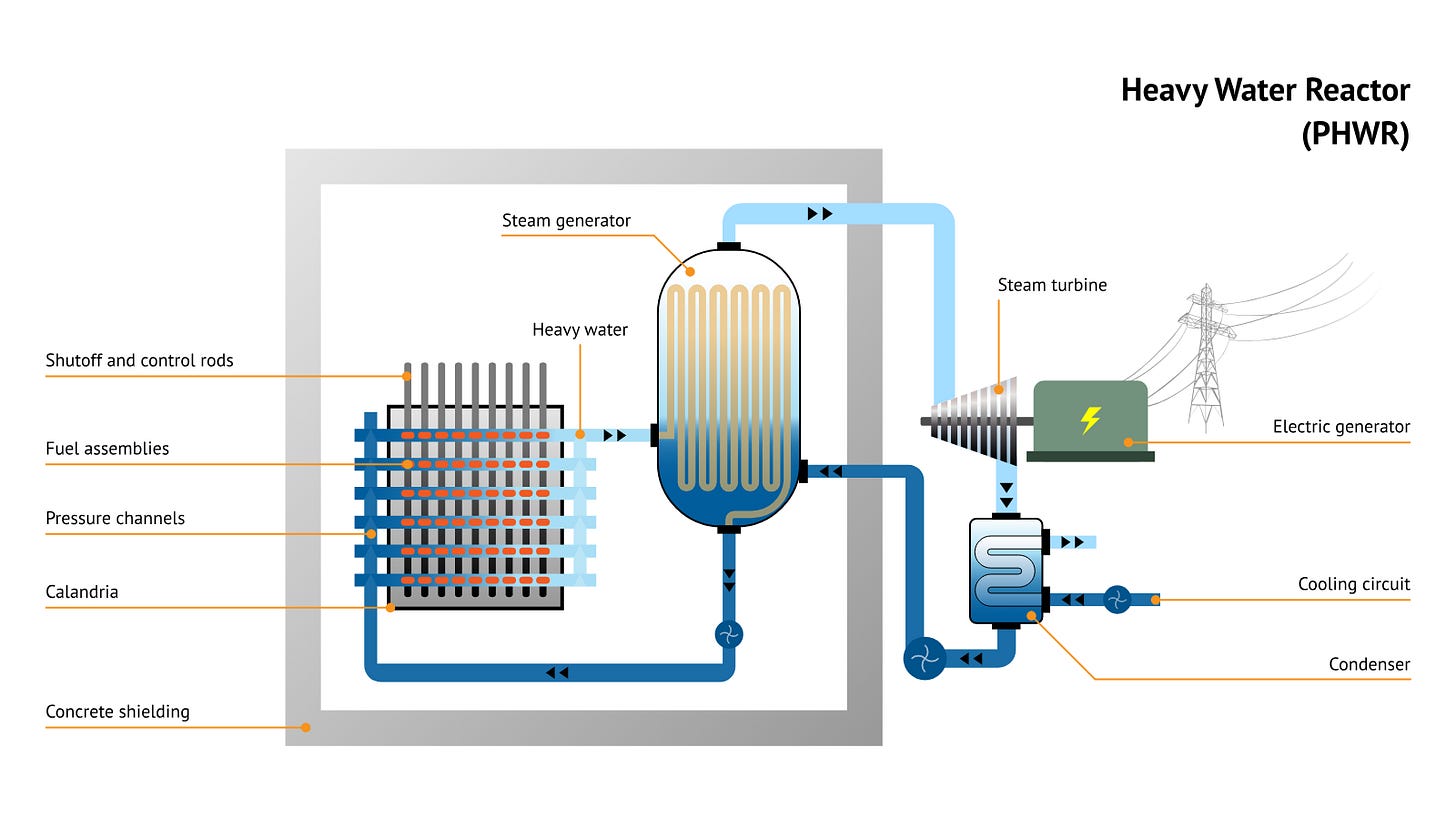
Moderator: heavy water
Coolant: heavy water
Operating temperature: 290 celsius
Thermal efficiency: 30 percent
Enrichment: 0.7 percent
A Pressurized Heavy Water Reactor (PHWR) uses deuterium oxide (heavy water) as both moderator and coolant instead of ordinary water. This allows the use of natural uranium (uranium-238), because the deuterium atoms in heavy water absorb significantly fewer neutrons than the hydrogen atoms in ordinary water.
The concept of heavy water moderation has been extensively trialled since the 1940s. Canada, India, and Argentina have all opted for PHWRs, as they allow countries to build reactors without relying on a uranium enrichment programme. Deuterium only makes up 0.0156 percent of hydrogen atoms in standard water and is extracted by circulating hydrogen sulfide gas between hot and cold towers to concentrate the naturally occurring deuterium.
PHWRs use separate systems for coolant (hot heavy water under pressure) and moderator (cold heavy water at low pressure) to maximize neutron efficiency. This separation requires hundreds of horizontal pressure tubes running through a large tank (calandria), with each fuel channel needing complex sealing connections and individual cooling circuits. While technically ingenious, this is builds in significant cost and complexity.
This cost of manufacturing and maintaining these hundreds of individual pressure tubes means that PHWRs remain relatively niche, providing only five percent of the world’s nuclear energy.
Advanced gas-cooled reactors
Moderator: graphite
Coolant: carbon dioxide
Operating temperature: 650 celsius
Thermal efficiency: 41 percent
Enrichment: 2.5-3.5 percent
Advanced gas-cooled reactors (AGRs) were the great hope of the British nuclear industry and served as the backbone of the UK’s nuclear fleet, building on the UK’s original gas-cooled Magnox reactors. While eight of the second-wave ‘advanced’ reactors remain in operation, the UK never succeeded in exporting the advanced design, and it exported only two of the original Magnox (though its plans were shared as part of the Atoms for Peace program, and the North Korean nuclear program was based on it).
They used carbon dioxide as a coolant and graphite as a moderator instead of water, which allowed the AGRs to operate at a higher temperature, providing a meaningful efficiency improvement over PWRs.
There was another advantage. In AGRs, the graphite moderator is a large, solid block in which the fuel channels are embedded. This made it theoretically possible to open individual fuel channels for refueling, while keeping the reactor running, as the graphite would stay in place and continue to slow neutrons effectively. By contrast, a water moderator involves the coolant cycling continuously, so its removal or disturbance during fuel handling would interfere with the moderation process, necessitating a shutdown for safe refueling.
Construction proved significantly more complex and expensive than expected and engineers later discovered that the graphite moderator was prone to cracking. It was also necessary to shut the reactor down for safe refueling.
While much maligned, the AGR was relatively cheap by the standards of British infrastructure mistakes. By the time they are all decommissioned in the 2030s, the UK will have gained fifty years of reliable electricity from these reactors, which collectively cost around £30 billion, significantly less than Sizewell C, and about as much as was spent on capping energy prices during recent energy price spikes.
Sodium-cooled fast reactor
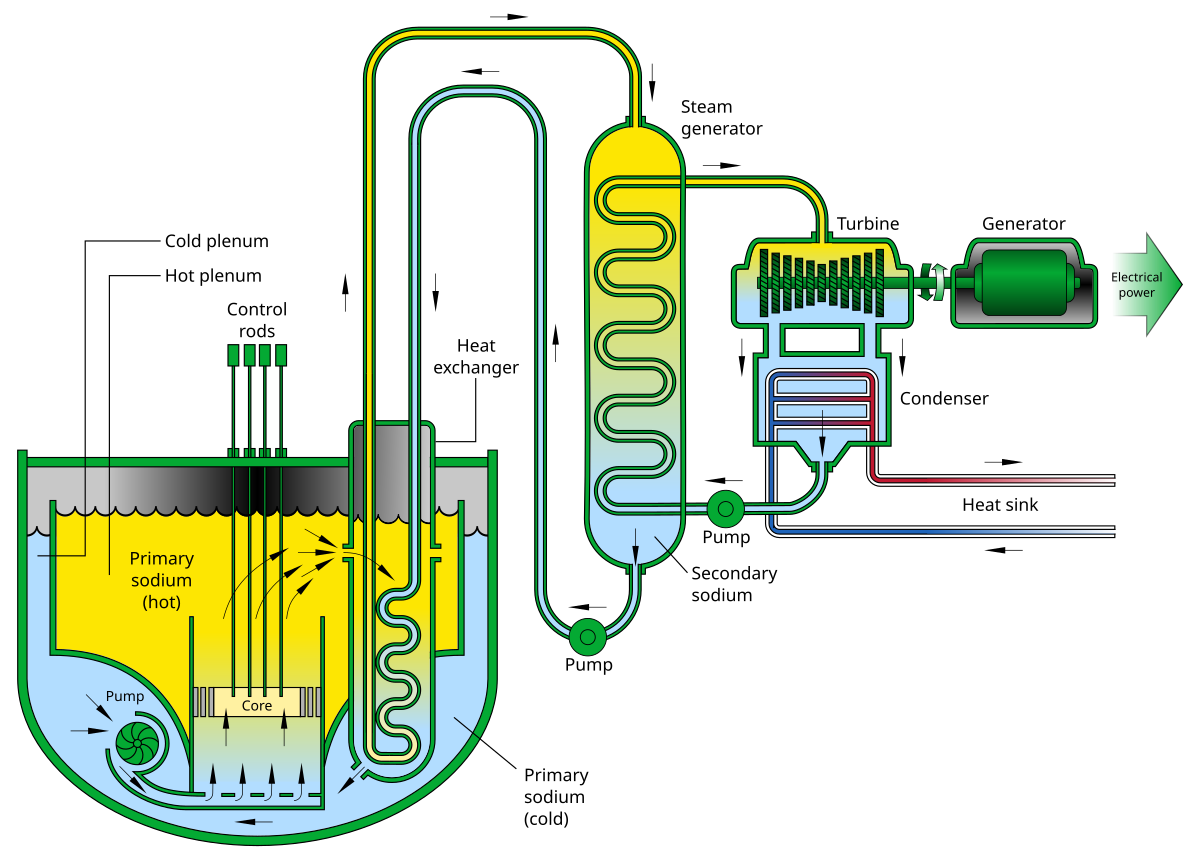
Moderator: none
Coolant: liquid sodium
Operating temperature: 550 celsius
Thermal efficiency: 41 percent
Enrichment: 15-30 percent
A Sodium-Cooled Fast Reactor (SFR) uses liquid sodium metal as its primary coolant instead of water. This allows the reactor to operate at much higher temperatures compared to traditional water-cooled reactors. The sodium coolant transfers heat efficiently and remains liquid without requiring high pressure. These higher temperatures significantly improve thermal efficiency, while the low pressure operation making maintenance simpler.
SFRs are among the only ‘fast breeder’ reactors to have ever been built. These reactors have the potential to produce more fissile material than they consume, theoretically making them self-sustaining after their initial fueling.
However, sodium's violent chemical reactivity with water and air presents serious safety challenges. The liquid metal ignites spontaneously in air and reacts explosively with water, requiring sophisticated containment systems, inert gas blankets, and multiple heat exchange barriers to prevent potential sodium fires.
The concept of sodium cooling has been extensively tested since the 1950s. Several countries have operated experimental and demonstration SFRs, including long-running plants like France's Phénix, Russia's BN-series, and Japan's Monju. A number of commercial projects are under construction, including TerraPower’s Natrium reactor in Wyoming.
Proposed or experimental reactor types
While the range in operational reactor design is quite limited, start-ups and government-funded R&D projects have been exploring a range of potential innovations. These are largely focused on finding alternative coolants to water so the reactor can operate with greater thermal efficiency.
There are few ‘original’ ideas in nuclear, so these concepts often rely on ideas that were explored during the 1960s or 1970s, but abandoned on the grounds of cost or complexity. Innovators are hoping that advances in engineering, technology, and material sciences can help to overcome some of these hurdles.
It’s important to note that the thermal efficiency numbers for these advanced concepts are R&D targets or design estimates – no reactor has ever demonstrated efficiency significantly above 40% at utility-scale.
Molten salt reactors
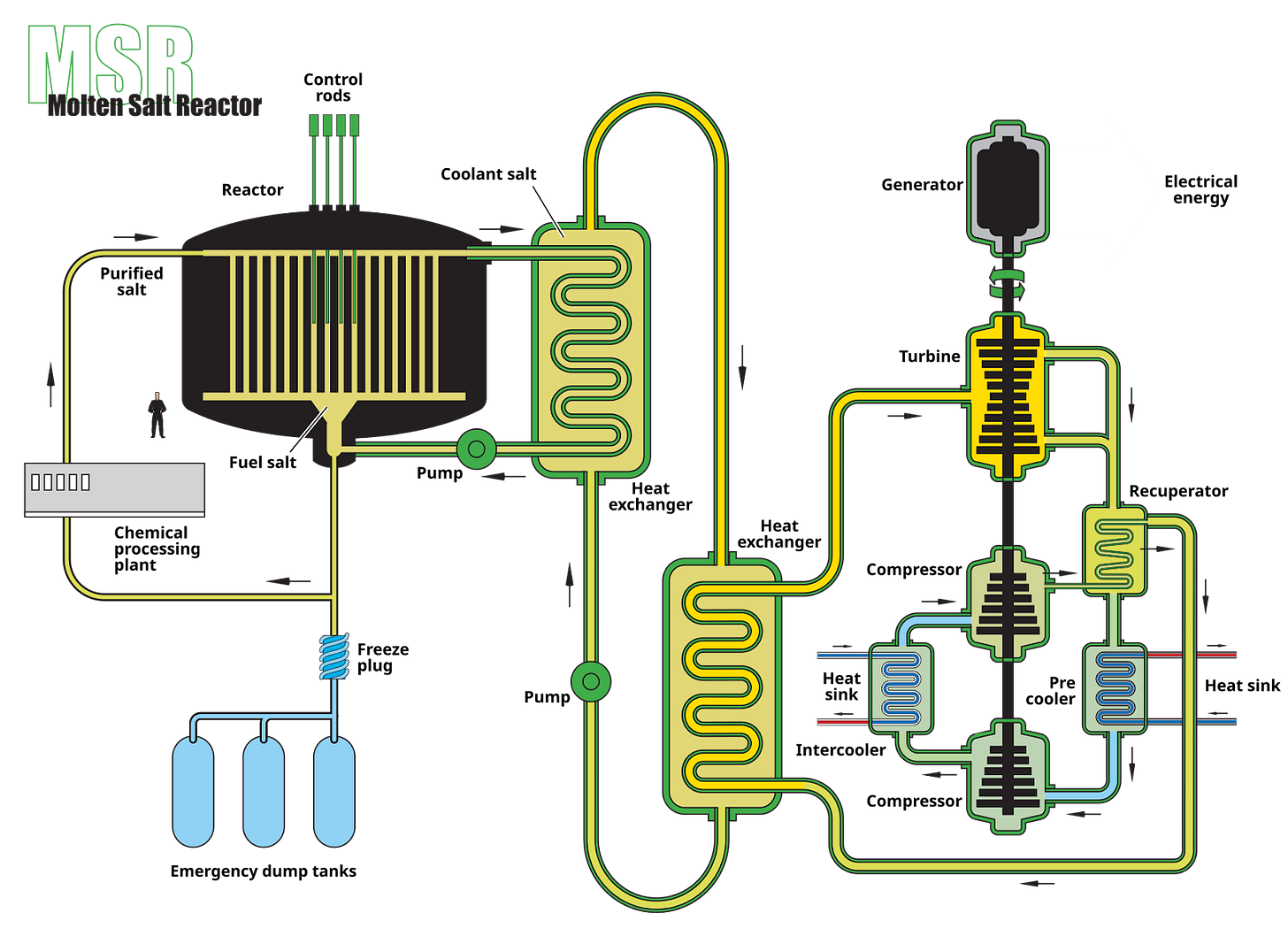
Moderator: molten salt
Coolant: molten salt
Operating temperature: 600-800 celsius
Thermal efficiency: 40-45 percent
Enrichment: 5-19 percent
A molten salt reactor uses a mixture of molten salts as its primary coolant and, in many designs, as the medium in which the nuclear fuel is dissolved. The molten salt stays liquid at high temperatures without needing high pressure, allowing efficient heat transfer without complex high-pressure systems. This allows the reactor to operate at much higher temperatures, typically around 700 degrees centigrade compared to traditional water-cooled reactors.
These higher temperatures improve efficiency, while the lack of pressurization reduces the likelihood of an explosion if the reactor malfunctions. Molten salts’ chemical properties can act as a passive safety feature. The molten salt keeps most fission products dissolved in the liquid and, if a leak occurred, would drain into a catch tank and quickly freeze, trapping the radioactivity. Because the salt boils only at around 1,400 celsius and carries heat well, the core can ride out a loss of active cooling for long periods without overheating.
The idea of using molten salt isn’t new. Oak Ridge National Laboratory deployed an experimental reactor between 1965 and 1969, but there was little incentive at the time to invest billions of dollars in commercializing them, given the success of light water reactors.
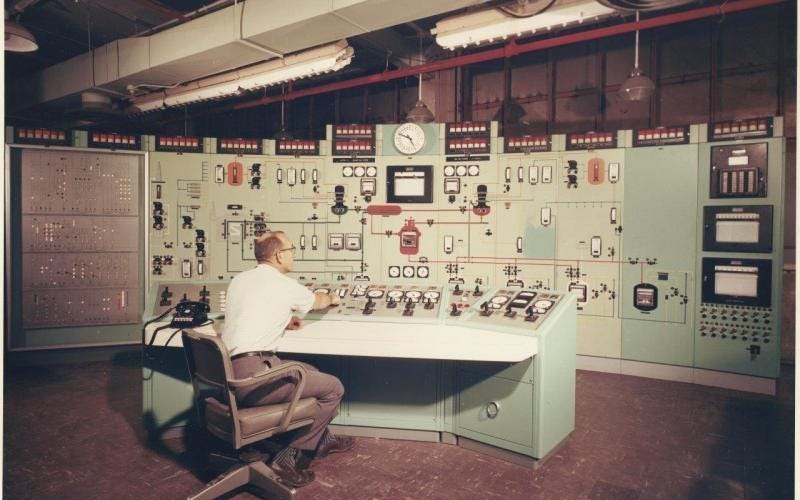
Governments are giving the technology a second look now and a number of start-ups are tackling the challenge. Google has struck an agreement to buy energy from Kairos Power, which is working on small molten salt reactors.
High-Temperature Gas-Cooled Reactor
Moderator: Graphite
Coolant: helium
Operating temperature: 750-950 celsius
Thermal efficiency: 48-51 percent
Enrichment: 17 percent
The High-Temperature Gas-Cooled Reactor (HTGR) uses helium gas as coolant and graphite as moderator. Helium is chemically inert and remains gaseous at high temperatures, which allows for high heat transfer without the risk of dangerous chemical reactions, while the graphite can absorb significant amounts of heat.
HTGRs use specialized fuel consisting of uranium particles coated with multiple layers of ceramic materials, which can withstand extreme temperatures while containing radioactive materials (even in case of a meltdown). There are two main design variants: prismatic block designs where hexagonal graphite blocks contain channels for fuel and coolant, and pebble-bed designs where tennis ball-sized fuel spheres move through the reactor core.
These high temperatures, however, require specialized materials and the specialised fuel particles require intricate manufacturing processes.
The US experimented with HTGRs, operating the Fort St. Vrain plant from 1979 to 1989. While the reactor itself worked, consistent faults in other parts of the plant’s setup led to its early decommissioning on economic grounds. There have also been experimental reactors in Germany and the UK. There is currently only one HTGR in operation globally, the pebble-bed Shidao Bay Nuclear Power Plant in Shandong province. Meanwhile, US start-up Valar Atomics is planning a test reactor in the Philippines.
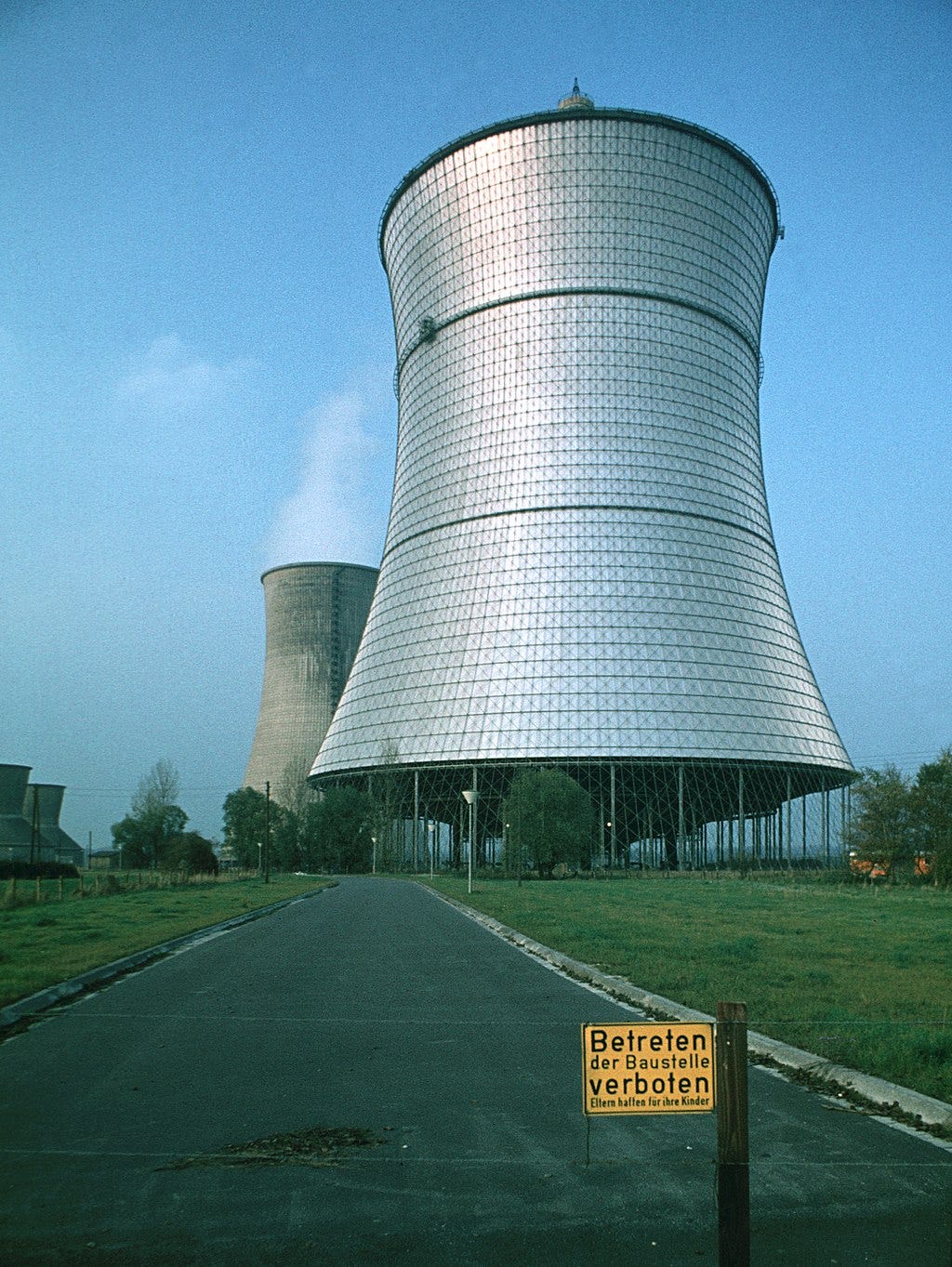
Lead-cooled fast reactors
Moderator: none
Coolant: liquid lead
Operating temperature: 480-580 celsius
Thermal efficiency: 42 percent
Enrichment: 16 percent
A Lead-Cooled Fast Reactor (LFR) uses liquid lead or lead-bismuth blend as its primary coolant instead of water or gas. This allows the reactor to operate at much higher temperatures, typically around 480-580 degrees celsius compared to traditional water-cooled reactors. The lead coolant remains liquid at these high temperatures without requiring high pressure, enabling efficient heat transfer while eliminating the need for complex high-pressure containment systems.
Lead also has some intrinsic advantages. It doesn't react violently with water or air, doesn't burn, and it effectively shields radiation. The high boiling point of lead (1,749 celsius) creates a substantial safety margin, as it's nearly impossible to boil the coolant during operation.
The concept of using liquid metal as a reactor coolant has been explored since the early days of nuclear power, with the Soviet Union pioneering lead-bismuth cooled reactors for their submarine fleet. However, this design comes with several challenges. The high density of lead creates substantial structural loading on reactor components. The coolant's opacity makes visual inspection of submerged components impossible, complicating maintenance. Additionally, lead's high melting point requires sophisticated heating systems to prevent freezing during shutdowns, which could damage reactor structures.
There are no LFRs currently in operation, but a few demonstrator reactors have been planned. For example, Belgium, Italy and Romania have formed a consortium with Westinghouse, although the project is in its early stages.
Supercritical Water Reactor
Moderator: Supercritical water
Coolant: Supercritical water
Operating temperature: 500-625 celsius
Thermal efficiency: 44-48 percent
Enrichment: 5-7 percent
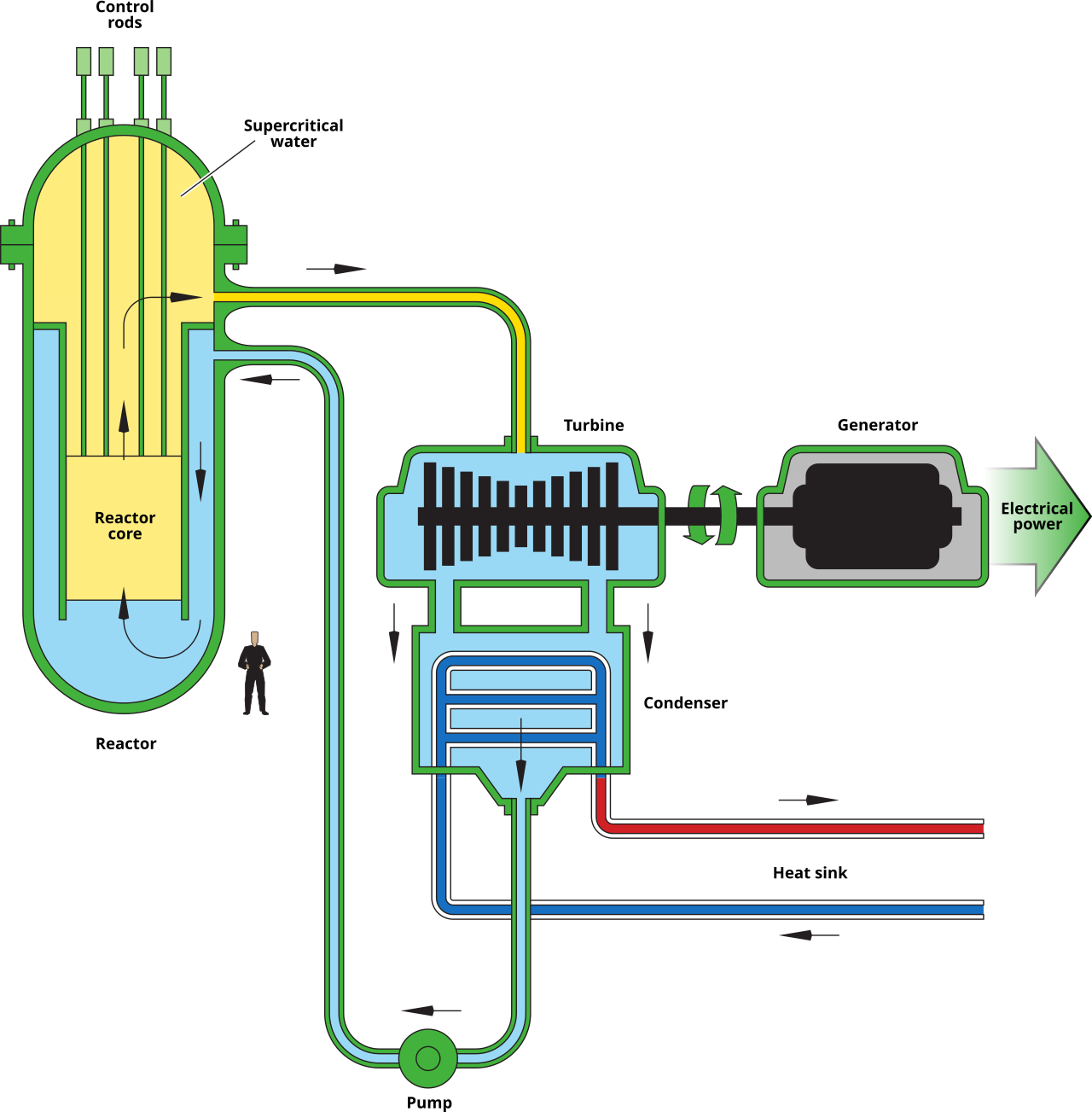
A Supercritical Water Reactor (SCWR) uses water heated and pressurized beyond its critical point (374 celsius and 22.1 megapascals) as both coolant and moderator. In this supercritical state, water has properties of both liquid and gas, with exceptional heat transfer capabilities. This allows the reactor to operate at significantly higher temperatures than many of its competitors.
These higher temperatures substantially improve thermal efficiency, but the extreme operating conditions create formidable materials challenges. Supercritical water's extreme temperature, pressure, and radiation exposure creates a powerfully corrosive environment that rapidly degrades conventional materials, necessitating specialized alloys for reactor components.
Several countries have research programs exploring SCWR designs, but the significant costs mean that technology remains at the conceptual and small-scale experimental stage.
Alex Chalmers is an editor at Works in Progress, focused on AI and energy. He’s also the author of Chalmermagne, a Substack covering technology, policy, and finance.